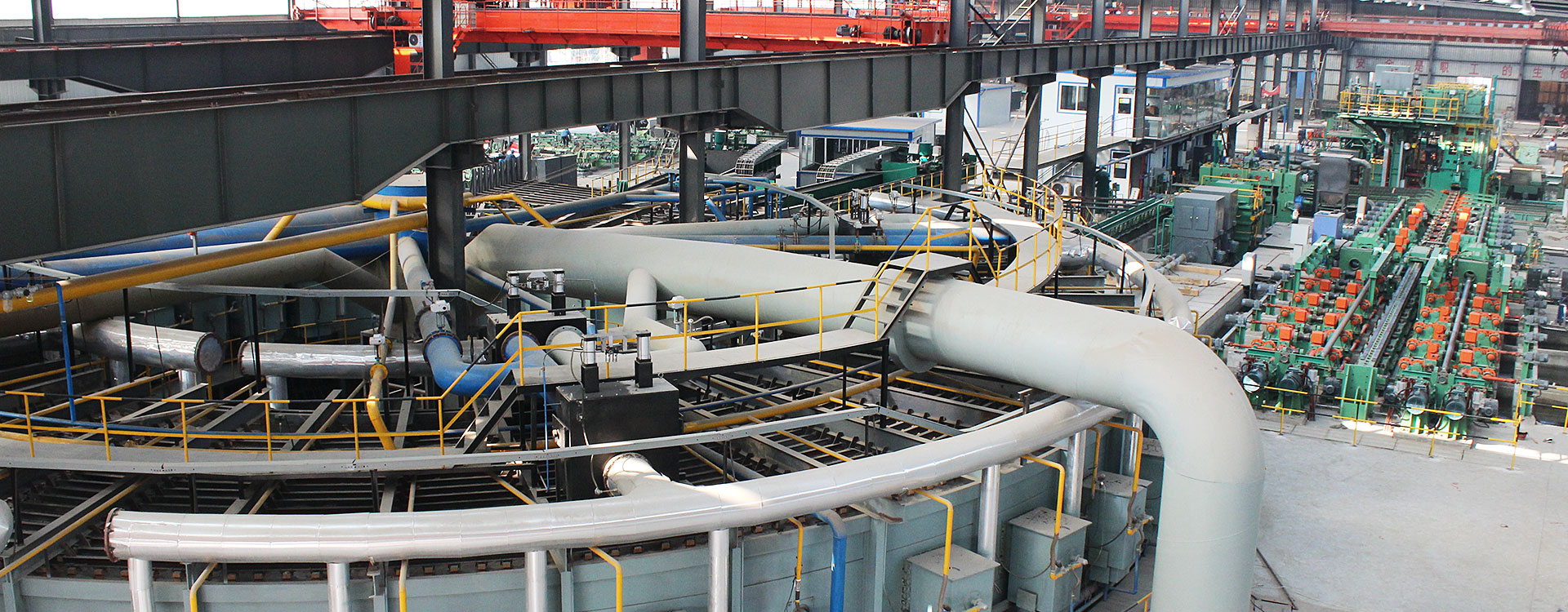
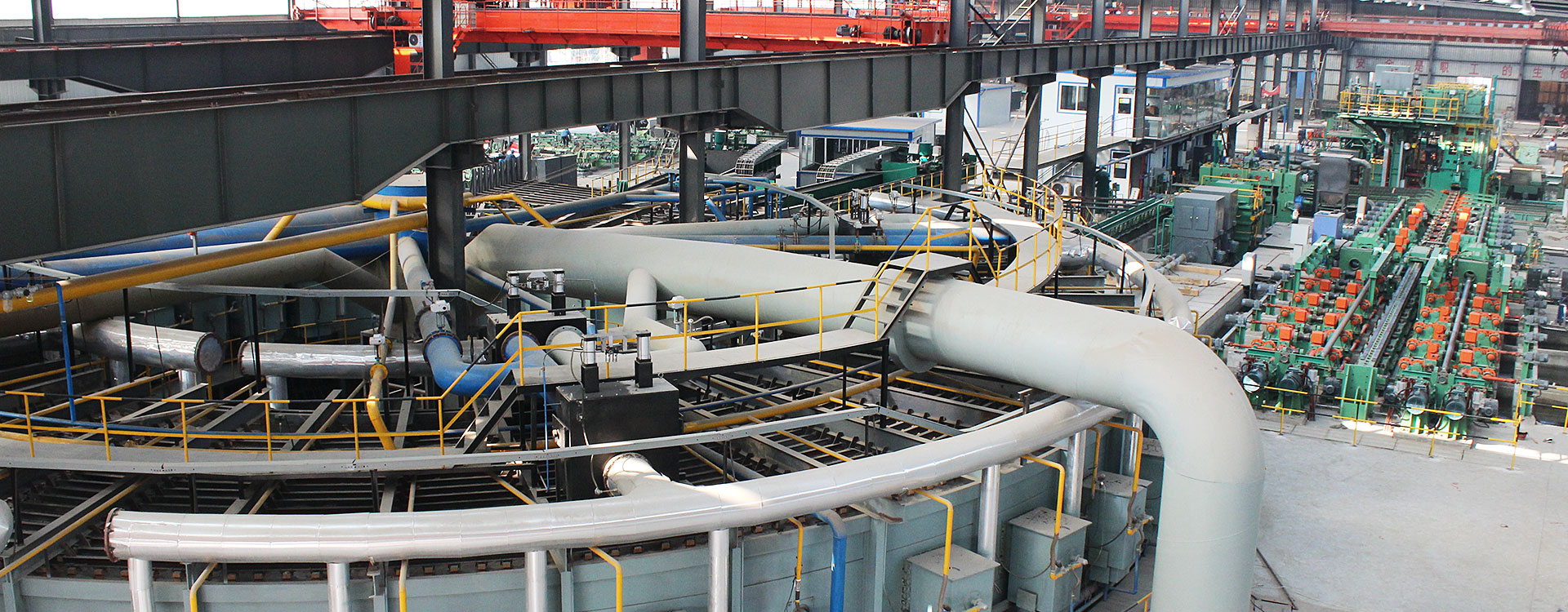
【概要描述】 In general, we use the diameter + wall thickness to describe the alloy seamless steel pipes. For example, if the diameter is 57mm and the wall thickness is 3mm, we denote it as "57x3". We typically use the inner diameter of the pipe, which is commonly ref
In general, we use the diameter + wall thickness to describe the alloy seamless steel pipes. For example, if the diameter is 57mm and the wall thickness is 3mm, we denote it as "57x3". We typically use the inner diameter of the pipe, which is commonly referred to as the nominal pressure inner diameter. For example, if the diameter is 57mm, it's denoted as "DN50". We use feet, which is commonly referred to as inches in plumbing, for example, if the diameter is 57mm, which is equivalent to 25.4mm, it's represented as "2 inches".
Calculation of alloy pipe weight: Weight per meter = (Diameter x Wall Thickness) x Wall Thickness x 0.02491 (for diameter and wall thickness in mm, weight in kg).
Welding and Processing Techniques: Before welding alloy pipes, they are preheated, and after welding, they undergo heat treatment and tempering. Prior to electric welding of alloy pipes, it's crucial to heat the pipes, and welding begins 30 minutes after reaching the controlled temperature. Temperature control during welding and the control of pseudo-beam temperature are automated through temperature control solutions. Heat treatment equipment employs far-infrared tracking plates.
An intelligent control system automatically sets and records trend graphs, accurately measures temperature, and heat transfer coefficients. When the temperature rises, the distance between the heat transfer coefficient measurement point and the edge of the weld is 15-20 millimeters. For welding to prevent deformation of alloy pipes, each column connection is welded symmetrically by two people, with welding extending from the management center to both sides. The weld seam is opened inside (close to the beam), and the operation process from start to finish—when welding the third layer of laminated pipes, it must be of a small standard, as its critical electric welding greatly affects welding deformation. When welding the first to third layers, planing must be done flat. After using carbon arc gas planer, grinding and polishing must be performed on the industrial equipment used for welding, and the surface layer of the weld seam must undergo nitriding treatment to make the surface metal shine, avoiding cracks caused by carbonization of the surface layer. Only the outer holes are welded, and the inner threads are not welded.
Electric welding = double-layer alloy pipes, and the welding direction should correspond to the laminated alloy seamless pipes, and so on. The spacing between each layer of welds is 15-20 millimeters. The welding current rate, welding speed, and the number of layers stacked must be consistent. When welding, start from the arc starting plate and end with the arc starting plate. After welding, seal control, grinding, and polishing, and clean the surface. After heat treatment and electric welding, tempering should be performed within 12 hours. If it's not possible to carry out heat treatment immediately, seek advice, provide thermal insulation and heat preservation, and slow cooling. During tempering treatment, measure the temperature values of the two heat transfer coefficients and weld on both sides of the welding.
Contact us
Shandong Lingying Steel Group Co., Ltd.
Tel:
+86-635-2113778
/
+86-635-2113779
Email:
lindacheng@lclxzd.com
Whatsapp: